- Applications
- ESD Testing
Electrostatic Discharge Testing and Simulations
Electrostatic discharge testing is utilized worldwide by electronics manufacturers to determine the ESD susceptibility of their devices. It is extremely difficult to estimate the exact cost of ESD loss annually, but it can safely be stated that ESD requires the development and testing of many hardware prototypes and contributes to a high number of warranty claims and loss of consumer confidence if failure occurs in the hands of the customer.
Given the high cost in time and materials associated with ESD hardware testing, the ability to simulate the ESD testing process in XFdtd is extremely valuable. Utilizing XFdtd's electrostatic discharge testing simulations allows engineers to pinpoint locations susceptible to ESD damage and optimize ESD mitigation during the concept and design stage of product development.
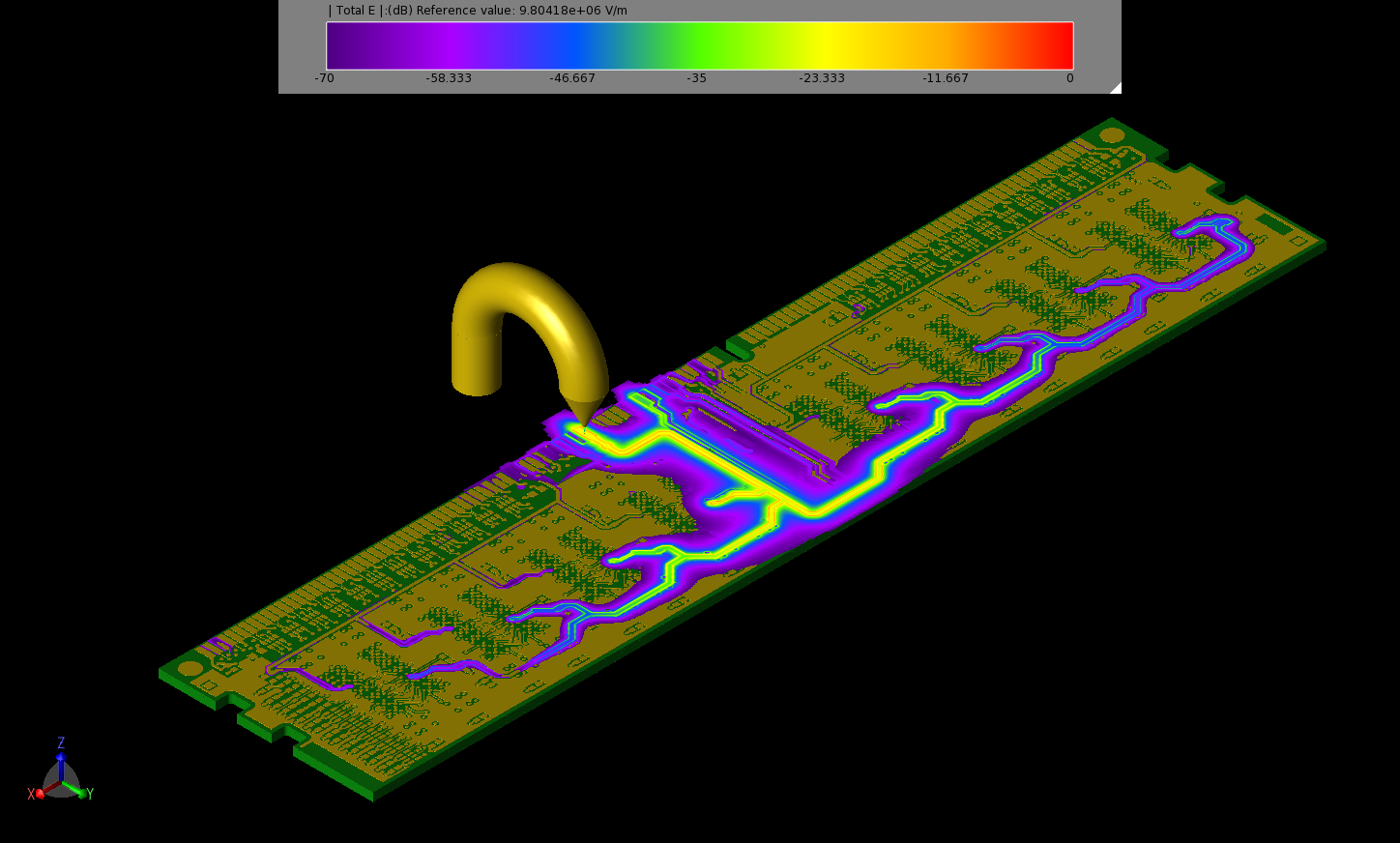
ESD testing simulation in XFdtd 3D EM Simulation Software
TVS Diodes
Integrated circuits are becoming more prevalent in the RF front end (RFFE) of devices. While they are supporting more functionality, they are also being reduced in size. The result is heightened susceptibility to ESD events and degradation. TVS diodes and other nonlinear ESD mitigation components protect the sensitive circuitry and redirect the strong ESD signals to ground before reaching the RFFE. XFdtd’s transient EM/circuit co-simulation capability allows these devices to be simulated in the full-wave environment where system-level analysis can be performed.
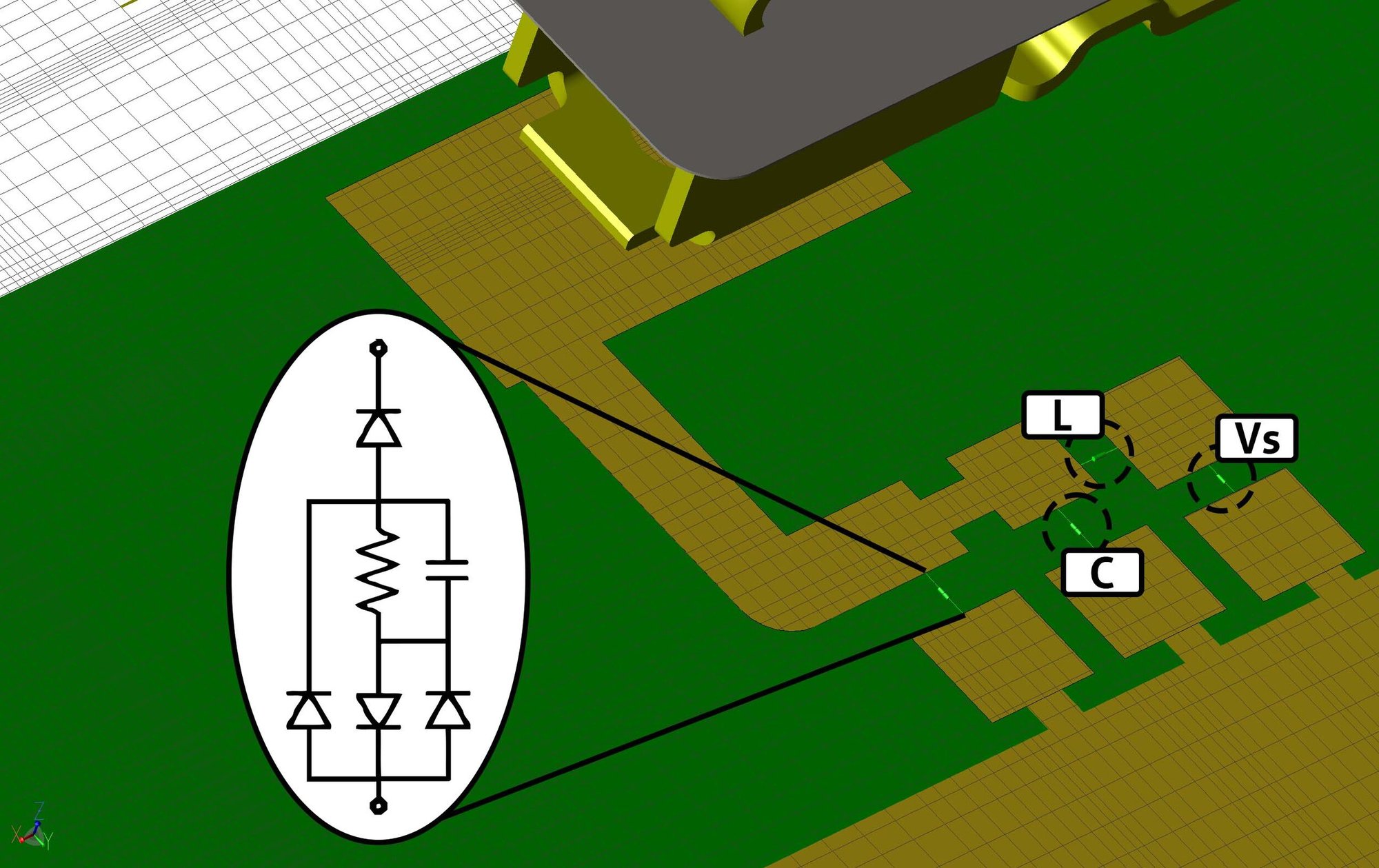
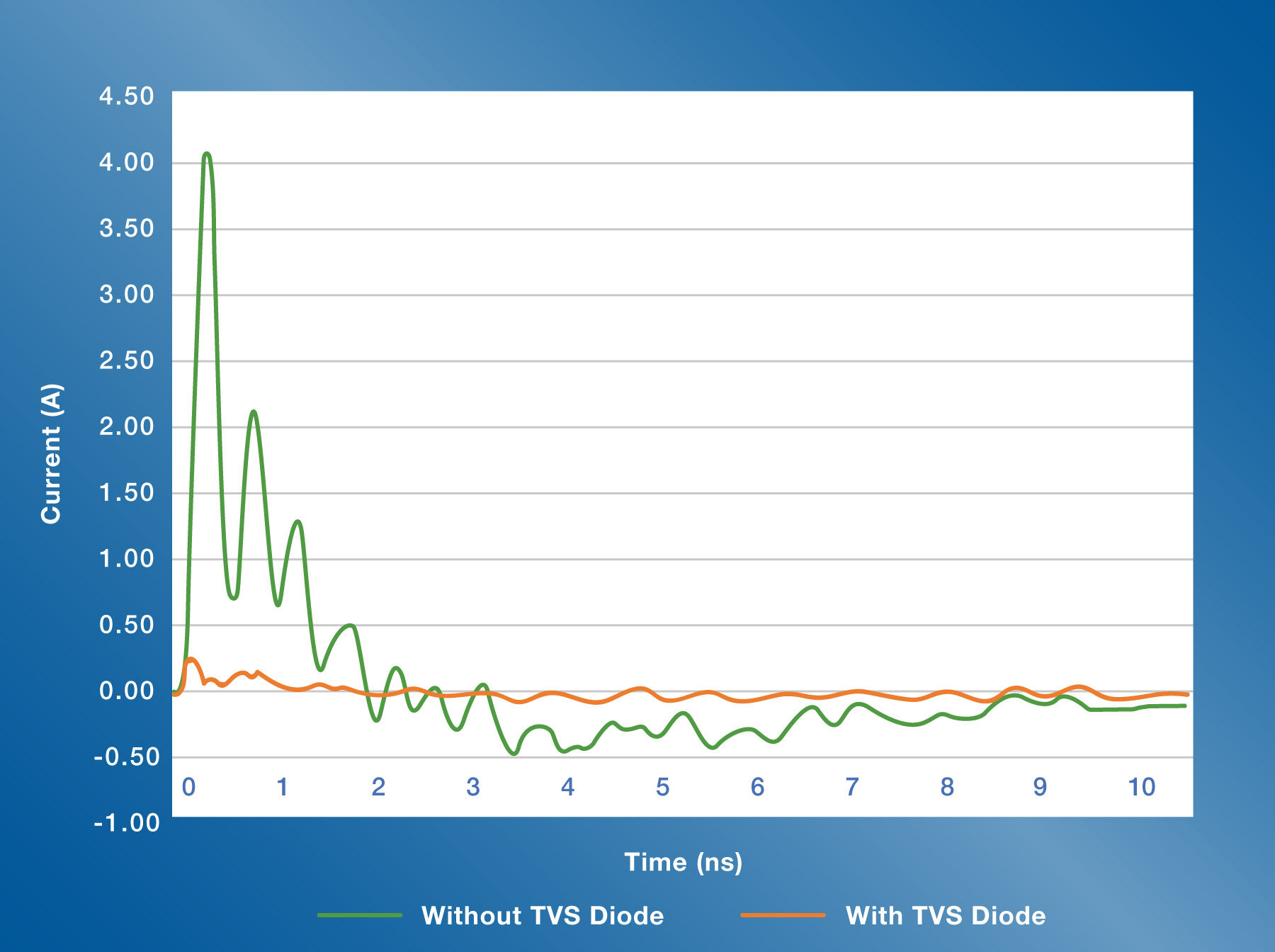
Dielectric Breakdown Prediction
Even for an experienced engineer it can be extremely challenging to pinpoint the location of an ESD failure during testing, and in some cases, to determine if a failure occurred at all. To solve this, the dielectric strength of materials can be defined in XFdtd. The dielectric strength of a material defines the maximum electric field it can withstand without experiencing dielectric breakdown (i.e., losing its insulating properties). Upon adding the dielectric strength of materials to an XFdtd project, it is possible to monitor FDTD cell edges for potential dielectric breakdown during transient simulations using a dielectric breakdown near field sensor. At the conclusion of an XFdtd simulation, cell edges which exceeded their dielectric strength can be easily located.
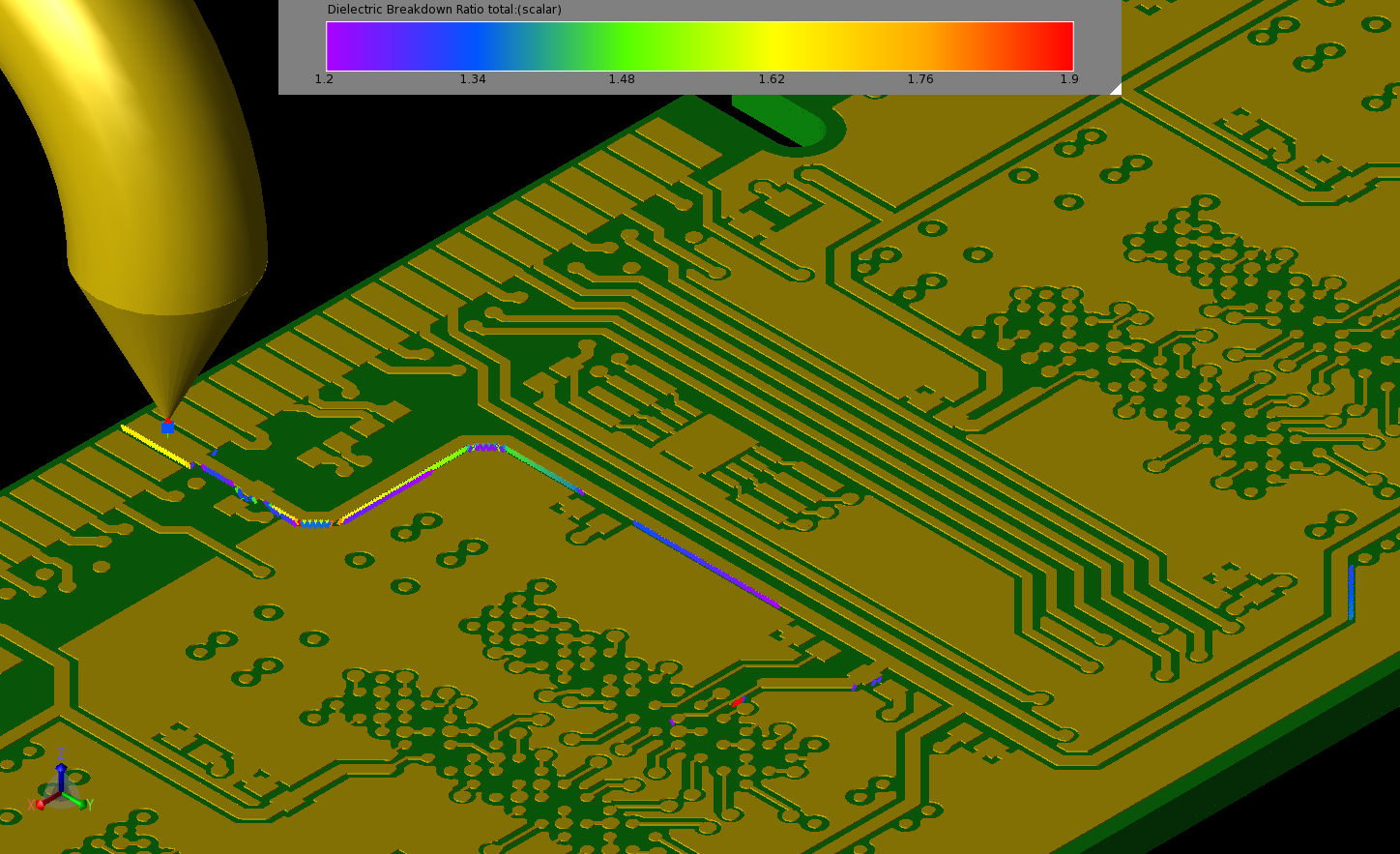
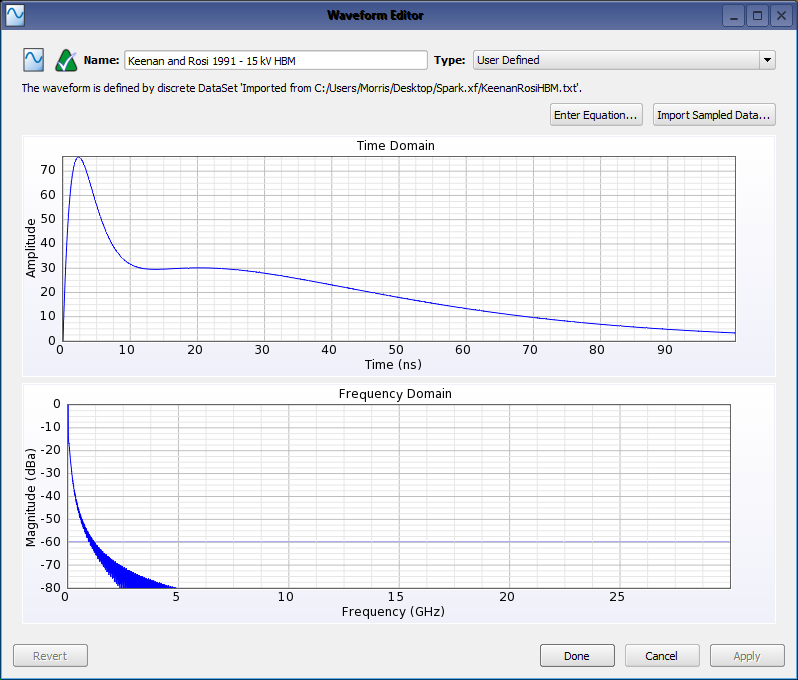
ESD Waveforms
ESD testing procedures and waveform models are defined by numerous standards from organizations including the American National Standards Institute (ANSI), JEDEC, and International Electrotechnical Commission (IEC), among others. The human body model (HBM), which approximates a discharge from a charged human fingertip to a grounded device, and the charged device model (CDM), which approximates a discharge from a charged device to another conducting object at a lower electrostatic potential, are the most common and widely used ESD models. These tests are generally performed using ESD Simulators, or ESD Guns, to apply high speed, high voltage pulses to various points of the device under test (DUT). Using XFdtd’s user defined waveform feature, engineers can import ESD waveforms defined by the various testing standards and use them to create ESD current sources in their XFdtd project. At this point, ESD simulator/gun models can be created and used to excite the DUT geometry at locations of interest and the resulting electromagnetic fields and current flows can be simulated and analyzed.
Circuit Component Overvoltages and Overcurrents
Generally speaking, circuit component failure is encountered more frequently than dielectric breakdown failure during ESD testing. To predict circuit component failures, rated voltage and current input parameters, which can be obtained from electronic component data sheets, can be added to XFdtd’s circuit component definitions. Upon completion of an XFdtd simulation, components that exceeded their rated design parameters are reported by XFdtd’s Max Component Voltages and Currents result dialog.
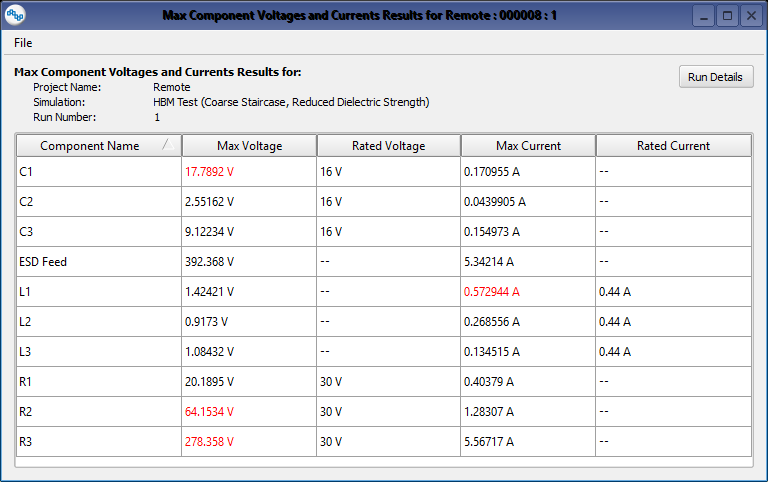
Optimize ESD Mitigation
While simulation cannot and should not entirely replace hardware testing, it can provide ESD engineers with insight into probable locations of ESD failure and will allow ESD mitigation designs to be optimized prior to the hardware prototyping stage. XFdtd’s ability to pinpoint locations at risk of experiencing dielectric breakdown and report circuit components exceeding their design parameters during an ESD event reduces product development costs and time to market, while improving product reliability and consumer confidence.
Additional Information
-
Webinars
XFdtd’s Transient EM/Circuit Co-Simulation for TVS Diode ESD Protection
In this webinar, learn how XFdtd's transient EM/circuit co-simulation effectively resolves ESD vulnerabilities earlier in the design process and prevents future certification setbacks.
Explore ResourceWebinars
ESD Testing and Damage Prediction Using XFdtd
This webinar introduces XF’s collection of ESD simulation features and demonstrates how to minimize the chance of undetected damage prior to hardware testing.
Explore Resource -
Videos
Demonstration of XFdtd's Electrostatic Discharge (ESD) Testing Features
Learn how to use XF's features for ESD testing as we walk through the process of analyzing a multi-layer PCB and identifying potential locations of dielectric breakdown.
Explore Resource -
Publications
Transient EM/Circuit Co-Simulation in XFdtd: A Closer Look at TVS Diodes for ESD Protection
This paper introduces XFdtd’s transient EM/circuit co-simulation capability, which combines the strength of 3D full-wave electromagnetic simulation with the flexibility of circuit solvers.
Explore ResourcePublications
Time Domain Simulation of Electrostatic Discharge Testing
This article from Microwave Journal introduces ESD simulation features in Remcom's full wave electromagnetic simulation software package, XFdtd. Learn about the time domain simulation of ESD testing.
Explore ResourcePublications
ESD Testing Simulation with XFdtd
XFdtd simulates ESD testing, enabling engineers to identify potential locations and components at risk of dielectric breakdown in their device designs prior to hardware testing. We summarize XFdtd's features to mitigate ESD risk.
Explore Resource
Save time and reduce costs.
Contact Remcom today for a customized solution to your most complex electromagnetic challenges.
Request a Quote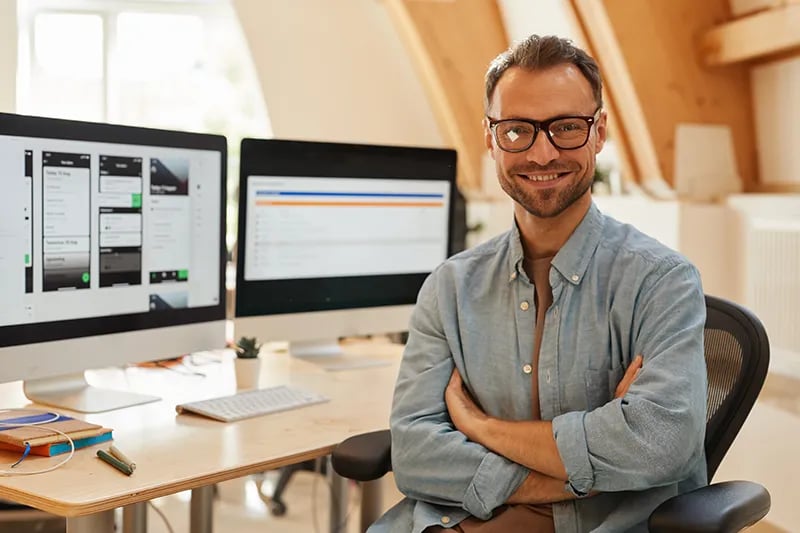